Bokaro wagon overhaul depot jackup outturn
Bokaro Wagon Overhaul Depot: on a longer haul
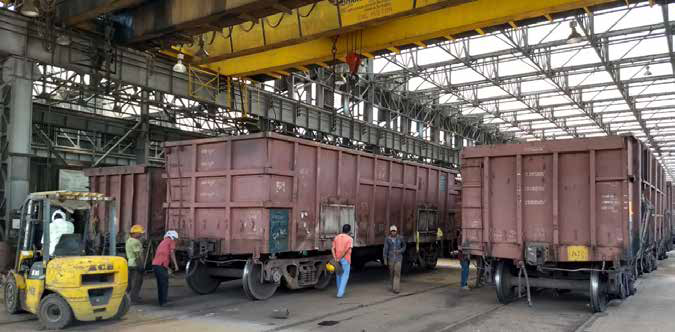
Bokaro wagon overhaul depot proposses to boost its wagon outturn in coming months. Railways Review reports
The premier, routine overhaul Bokaro wagon depot under Adra division of South Eastern Railway (SER) proposes to raise the wagon outturn to 450 units in the coming months, up from 300 units at present. The depot overhauls, open BOXN, BRN, BOXNHL, and BOSTHS wagons.
The higher outturn will be delivered following the expansion of the depot shed 120 meters from 100 meters at present. Bokaro ROH depot, set up in 1992, is highly instrumental in ensuring wagon availability, mainly for transporting coking and non-coking coal, the prime raw materials to the primary and secondary steel and plants, located on the South Eastern, Eastern, East Coast, and East Central Railway Zones. Requirements of wagons are immense in the concerned zonal circuit. This is due to the fact that, coal haulage is the prime earner for the Railways. Hence, any non-availability of wagons due to failure or accidents, resulting in higher detention can be hardly afforded by Indian Railways.
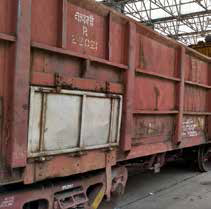
Earlier bulged and damaged door fully repaired and fitted by the depot on BOXN wagon.
To ensure higher availability of wagons and curtail detention, the depot has recently installed, door straightening device. This is a unique device. It exerts required pressure on the door hinge of the wagons for straightening the doors. Bent doors can cause significant disruptions during wagon tippling, creating higher levels of detentions in the steel and power plants premises. Given bent doors, the wagons would be required to be decoupled and shunted out from the rake. This is as because bent doors can cause disruptions in the functioning of the tippler. Most significantly, it can damage the walls of the tipplers as well. This could further contribute towards severe time lag if there are a number of wagons in the rake, with bent doors set for tippling.
CRITICAL REPAIRS
The routine overhaul undertaken by the depot consists of complete body lift, bogie drains out, de wheeling, followed by sending the wheels to the wheel profiling shops, followed by thorough examination and turning the wheel on the wheel lathe. Ultra sonic tests are carried on the axles. For reliability of the wheel sets, tests are performed on the centre cartridge roller bearings. For bogie rack detection, DPT tests are undertaken followed by load bearing tests. On the draft gears, DPT tests are undertaken on the knuckle and the couplers. For ensuring safety, critical air brake testing, involving both sensitivity and insensitivity tests are performed on the brake cylinders and distribution valves. This is to detect any leakage in the cylinders or the brake pipes.
Followed by the necessary tests and repairs, fitment of the bogie, along with the wheel sets is carried in the superstructure.
Appropriate repair of the body attains large scale importance at Bokaro depot. Complete sidewall, end panel and floor repairs are undertaken. For higher reliability of the sidewalls, plates are now being replaced from earlier 5 mm to 6 mm involving stainless steel from earlier mild steel. Stainless steel will prevent corrosion in a major way.
While comprehensive ROH is performed by the depot after every span of one and half years, Bokaro wagon depot has an adjacent maintenance facility. This carries out emergency welding work on the wagons damaged during loading and unloading. Close to 700 open wagons are repaired every month at the parallel depot.